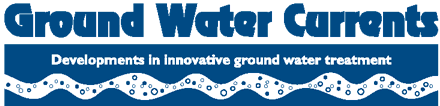
From Ground Water Currents, April 1995, Issue No. 11
Bioreactor and membrane for VOCs
By Daniel Sullivan, EPA Risk Reduction Engineering Laboratory
The ZenoGem process is an integrated bioreactor andultrafiltration (UF) membrane system that is designed to removebiodegradable materials, including most organic contaminants, from ground water and wastewater. The ZenoGem technology was evaluated at a Superfund Innovative Technology Evaluation (SITE)Program demonstration at the Nascolite Superfund site in New Jersey. The ground water at this 17.5 acre site had been contaminated from past operations at the facility, which included manufacturing of polymethyl methacrylate plastic sheets, commonly known as plexiglass. Methyl methacrylate (MMA) is the major contaminant at the site, with ground water levels approximating 12,000 milligrams per liter (mg/L). In addition to the other volatile organic compounds at the site, chemical oxygen demand (COD) levels often approximated 20,000 mg/L. The ZenoGem SITE demonstration achieved 100% removal of MMA and between 84% and 95% for COD.
Here's how ZenoGem works. The wastewater enters the enclosed tank bioreactor where a biomass containing bacterial culturesbreaks down the organic contaminants. In order to maintain sufficient aerobic conditions and optimal process temperatures, the contents are constantly mixed by the introduction of air bubbles through a series of manifolds from the tank bottom. Airis recycled, except for the air that is emitted into the atmosphere through a pressure purge vent, but not before it first passes through a carbon adsorption unit.
Feed flow wastewater treated in the bioreactor is continuously fed into the UF membrane system. The membrane system consists ofa series of tubes, in ten foot modules and approximately three inches in diameter, into which the cylindrical membrane filtersare inserted. UF is a pressure-driven cross flow filtration process (typically at 60 to 70 pounds per square inch) in whichthe water to be processed flows tangentially over the surface of the membrane filter that is capable of separating both insoluble materials (bacteria, colloids, suspended solids) and higher molecular weight soluble materials from the treated water. Thus,the treated filtrate from the bioreactor flows through the membrane while the remaining feed, a mixture of sludge solids and unfiltered wastewater, is concentrated and recycled to the bioreactor where it remains in the treatment system for further treatment for several weeks. Because of the long sludge retention time, the bioreactor size is significantly reduced.
The SITE evaluation ran for 89 days. During the evaluation, shock loading tests were performed that demonstrated the flexibility of the process to handle a sudden increase (a four-fold increase) of concentration of contaminants. Overall, the process ran very smoothly and could recover quickly from upsets encountered in Superfund operations such as loss of electricity, quadrupling of feed concentration, free product in feedstock and adverse weather conditions. The system was computer controlled with an alarm that activated a beeper retained by the operator, demonstrating that unattended operationis extremely viable for extended periods.
The resulting treated water product from the process was clear,odorless and free of suspended solids. For this project, the product was sent to the publicly owned treatment works (POTW) which accepted the product for disposal at $22.50 per 6,000gallon tanker. The bioreactor, which had processed approximately 28,000 gallons of water, contained only 400 gallons of nonhazardous sludge at the end of the 89 day period. The sludge was stabilized and sent to a landfill.
For more information, call Dan Sullivan at EPA's Risk Reduction Engineering Laboratory at 908-321-6677.